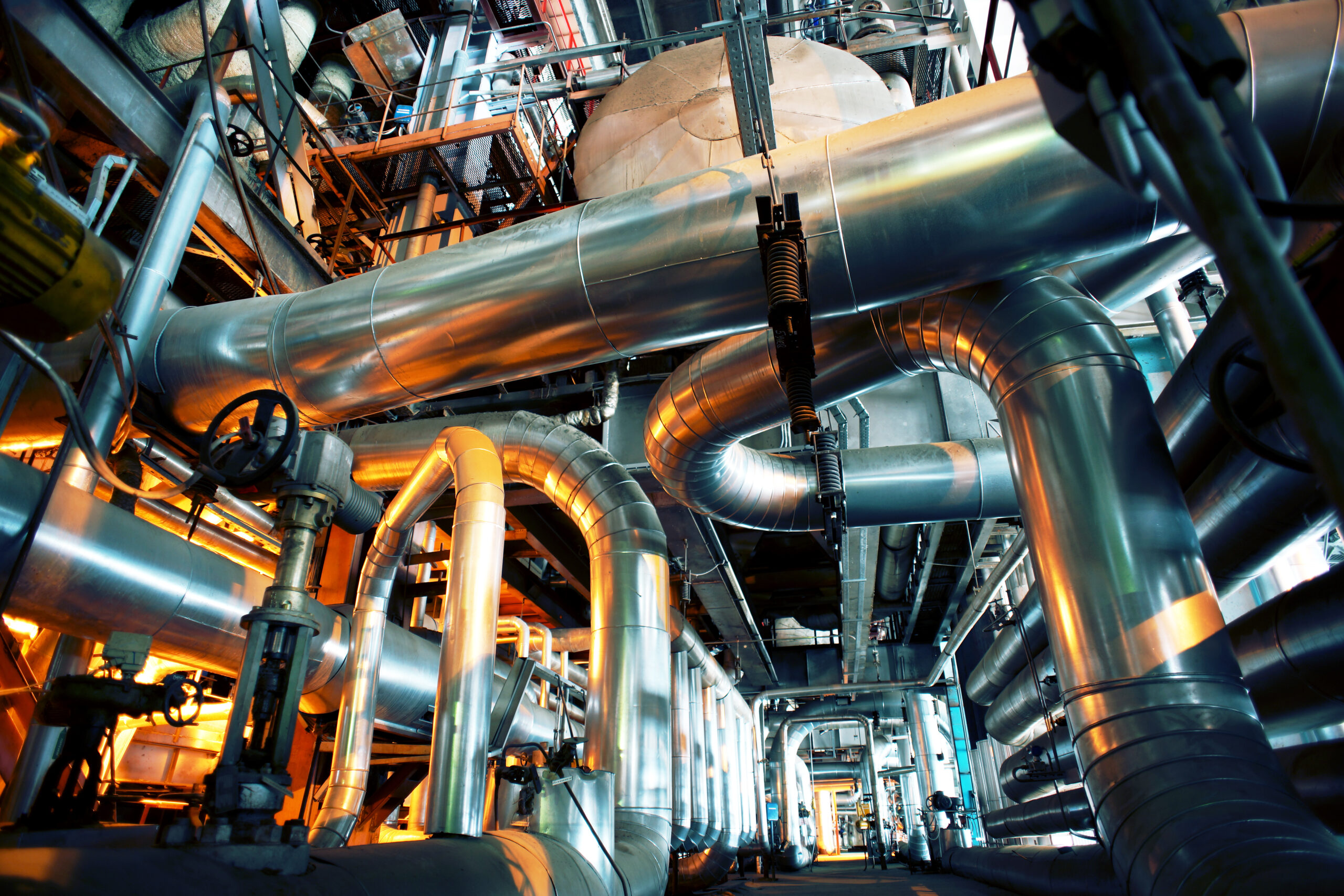
Root Cause Oscillation Diagnosis
Challenge
Troubleshooting cause and effect relationships related to the variability of key process signals is time-intensive for process control engineers. It can be difficult to determine the root causes of variability due to the complexity of modern manufacturing processes.
Modern manufacturing processes may include hundreds of measurements and the variability path can be masked by process features such as recycles and heat integration. These additional considerations add a significant amount of time to cause and effect determination, and can make manual, visual analysis an impossibility.
In this particular use case, a published industrial dataset from a minerals concentrator plant operation is utilized. In the plant, an oscillation originated just upstream of the first cells in the flotation circuit, and the automatic control strategy then propagated the oscillations through the circuit. The causal maps produced by the Causality Add-on correctly guide the user to the true oscillation source.
Solution
Causality, a Seeq Add-on, generates causal maps using a statistical algorithm. Each circle on the map represents a signal, the causal flow between each signal is represented through arrows.
The smaller red circles represent the most dependent signals (effects) while the larger, blue circles represent the most independent signals (causes).
The Causality Add-on goes beyond correlation analysis to statistically distinguish cause and effect whereas correlation analysis alone only identifies time-lagged dynamic correlations.
Solutions
Analytics tools that identify cause and effect relationships greatly reduce the list of potential causes, provide significant time savings, and increase potential profitability.
In addition to the analysis time savings, the causal relationships discovered may provide key insights necessary for process and control strategy performance improvements. In some cases, the root cause of process variation is directly diagnosed by the causal map, and the process changes or maintenance needed to resolve the issues, can be planned.
Data Sources
- Process Data Historian: OSIsoft PI, PHD, many others
- Information pulled from published literature dataset for an industrial minerals concentrator plant
Data Cleansing
- The user creates a dataset for analysis on a single worksheet in Seeq Workbench, removing downtime data and selecting a representative time period where the variability to be analyzed is consistent across the time range. The remainder of the data cleansing for this use case occurs automatically and is guided by the user during the root cause analysis.
- The Signal Preprocessing component requires numeric signals and generates evenly sampled data across the dataset for the causality analysis. It flags signals that are not appropriate for the causality algorithm (e.g., discrete signals, string signals, sparsely sampled signals, etc.)
- The Signal Downselection component excludes redundant signals by identifying multicollinearity among the signals
Calculations & Conditions
- Casual map produced through statistical analysis of the cleansed, condensed dataset created through preprocessing and downselection
- Variation of causality parameters (statistical relationship sensitivities) across the range to determine the consensus root cause among the signals, is controlled by the user
- User filters causal map display based on their process understanding and troubleshooting goals
Reporting & Collaboration
Seeq Organizer documents the causal map alongside process data trends and other associated analytics, for a more holistic view of the manufacturing process. This allows for operations personnel to discuss findings and incorporate them into the process improvement workflow and overall decision support.
Causal maps can be compared across different time periods to more easily detect shifts in process behavior.