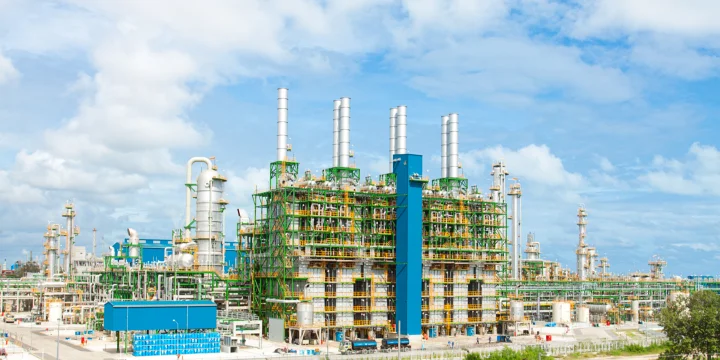
Online Furnace Conversion
Challenge
Making an accurate prediction for real-time furnace ethane conversion is critical to maintaining effluent purity and resulting ethylene production rates. Overestimation of conversion leads to undershooting production targets and lost opportunity. Underestimation can lead to overproduction, overloading downstream units or increasing inventory storage costs. For a large-scale petrochemical manufacturer, conversion calculations were complicated, typically performed offline, and required manual calculation each time a new weekly lab sample was received.
Solution
An online version of the existing furnace conversion calculation script was implemented using Seeq’s external calculation function. The actual conversion was compared to the online prediction signal and large deviations were flagged. Asset Tree functionalities were used to perform the calculations on a single furnace and then quickly scaled to all site furnaces, with results summarized for all furnaces in a dashboard. Auto-updates were configured so that anytime users open the dashboard, they see the furnace conversion and comparison calculations for each new lab sample received. They can then make decisions as to whether the predicted conversion signal, a value calculated in the plant’s distributed control system, should undergo a bias adjustment to better reflect recent data.
Results
This improvement eliminated the need for SMEs to manually calculate the furnace conversion, saving time, and ensured the calculation was performed for every lab sample received. When a high delta between the actual and predicted conversion is observed, the process engineers take proactive actions to adjust the predicted conversion signal calculation. This provides operators with an accurate account of ethylene production rate and allows them to make rate bumps when necessary to keep production rate at target. Recently, one site observed more than 1 million pounds of production losses due to running below target production rates when they believed they were on target. Since the implementation of the online calculation, they have seen less than half of these losses, projecting a year-on-year revenue improvement of more than $250,000.
Data Sources
- Process Data Historian (OSIsoft PI, AspenTech IP21, Honeywell PHD, etc.)
- OSIsoft Asset Framework or other asset hierarchy
- LIMS (Lab Information Management System)
Data Cleansing
- Process data signals were cleansed to include only data with timestamps matching lab data timestamps
Calculations and Conditions
- Lab data and process data from different data sources were overlaid in Seeq Workbench.
- Seeq Formula was used to call the external conversion calculation script for calculating actual values from the process data and lab data, eliminating the need for manual calculation any time a new lab value is received.
- Scorecard metrics showed the delta between the actual and predicted furnace conversion at the time of each lab sample and used priority color thresholds to draw attention to high deviations.
- An asset structure was built for these calculations using Seeq Data Lab.
- Treemaps were used to view current predictor status across all furnace assets.
Reporting and Collaboration
Results were summarized for all furnaces in a dashboard. With configured auto-updates, users see the furnace conversion and comparison calculations for each new lab sample received upon opening. They can make immediate and accurate decisions as to whether the predicted conversion signal needs a bias adjustment to better reflect recent data.