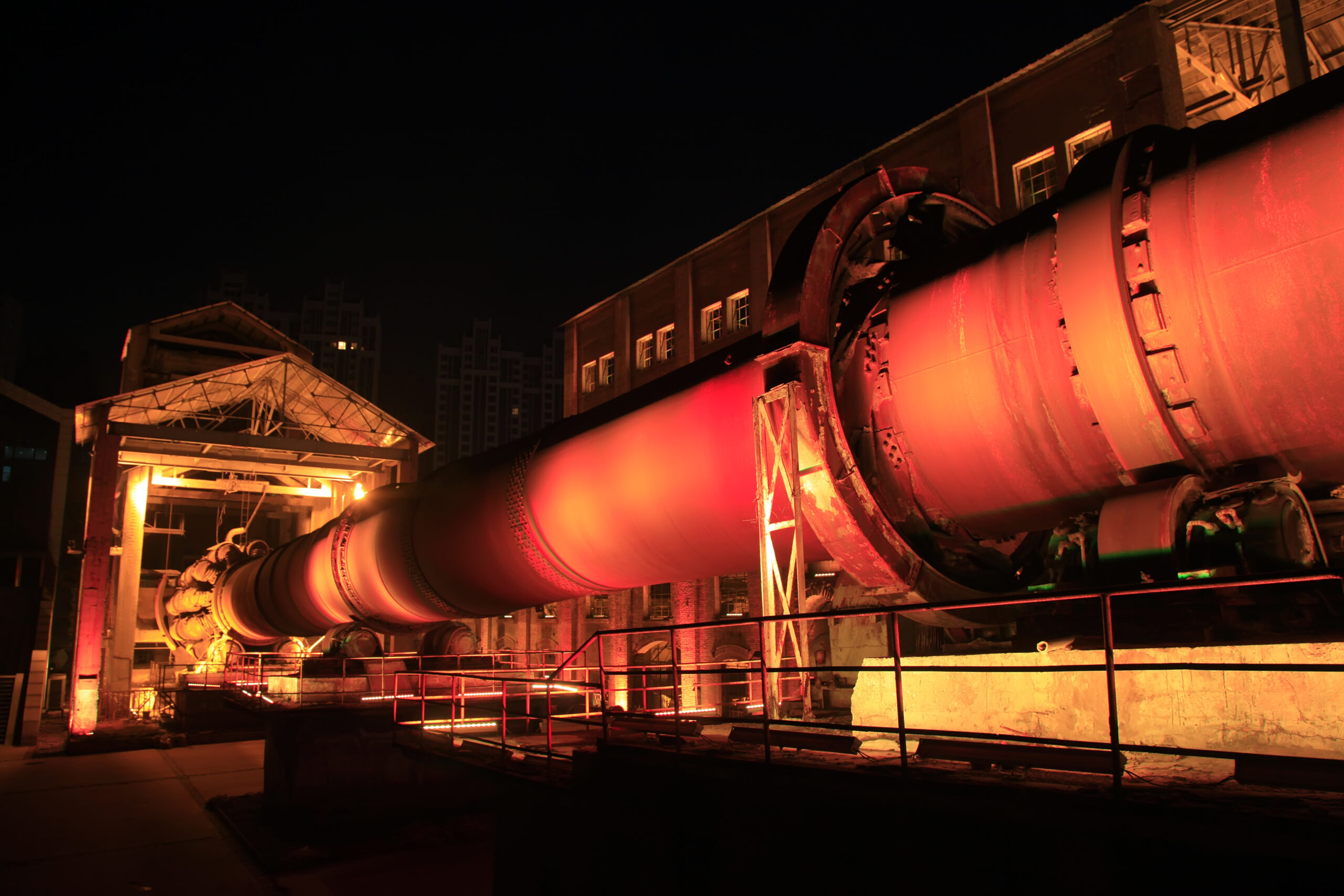
Kiln Stoppage Root Cause Analysis
Challenge
An S&P 500 supplier and aggregator of heavy building materials was experiencing unexplained episodes of kiln stoppage. In one instance there were two multi-hour stoppages in a five-day period, though unplanned stoppages typically happen about once a quarter. The situation was causing expensive production loss.
Cement kilns can stop unexpectedly for a wide variety of reasons, such as an induced draft bearing fan failure, high pressure due to a blockage or chemical incompatibility. Unexpected stoppages are unacceptable as they can cost the cement operation $20,000 per hour in production loss so it is critical to understand why they occur and what can be done to prevent them in the future. The building company needed to be able to identify stoppage events and investigate the data leading up to the stoppage for root cause analysis.
The company’s engineers were attempting to do analysis via Excel spreadsheets. The engineering team would look at charts and create reports but the analysis was cumbersome and not sufficient to get to the bottom of the kiln stoppage events.
Solution
Using Seeq advanced analytics, the company’s process engineer searches the kiln feed signal and identifies times when the kiln went down. Using Seeq Workbench, the process engineering manager can zoom in to the timeframes just before the unplanned stoppage to investigate the cause. The manager can also quickly and easily compare multiple stoppage events to determine if the same cause of failure has contributed to multiple stoppages.
Data Sources
- Process Data Historian: Wonderware
Data Cleansing
- The Kiln Feed Flow signal is filtered using Seeq’s agile filter to smooth the signal.
Calculations & Conditions
Seeq’s Value Search tool creates capsules for stoppage events when the Kiln Feed Flow is low
Reporting & Collaboration
- The Seeq Organizer Topic is configured to auto-update as new data streams in to notify the operator on new stoppage events.
Results
The process engineering manager can share the findings with others on the team, including the production manager, to get input and to suggest mitigations. The whole team can collaborate and monitor all stoppages to determine if they were planned or unplanned. Any time a common root cause comes to light, the team can change the process and then monitor it for the desired outcomes. This reduces the likelihood of unplanned outages and, therefore, the cost of production loss.