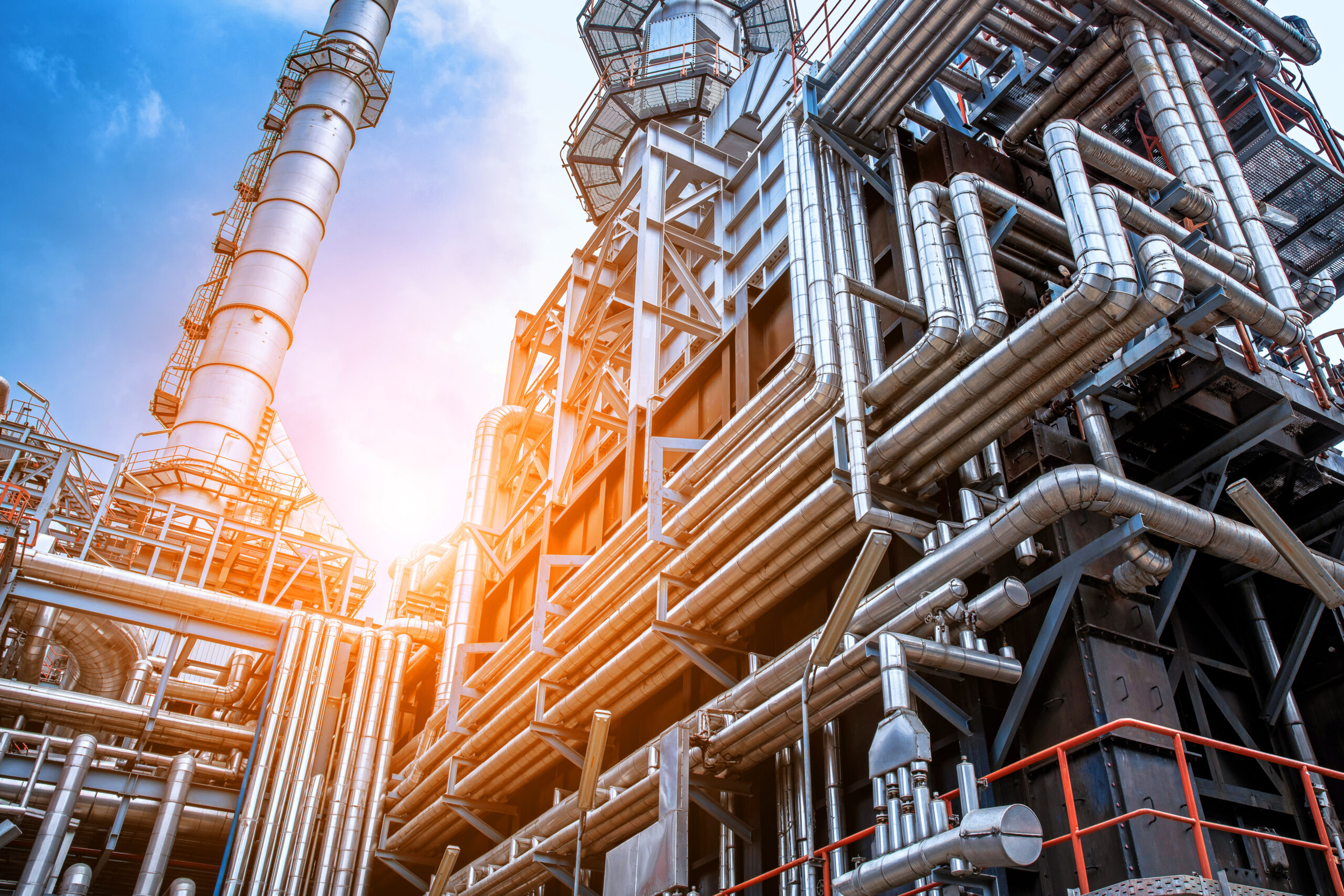
Heat Exchanger Monitoring—Predictive Analytics for Maintenance
Challenge
Heat exchangers play a crucial role in the downstream oil & gas industry. Prior to distillation, crude oil is heated through a series of exchangers called the preheat train. Additionally, heat exchangers are used to heat intermediate feeds prior to processing in various reactors.
As oil flows through the heat exchanger, deposits on the internal surfaces cause fouling, affecting the ability to transfer heat. In order to maintain the outlet temperature, the heat exchanger must be run at reduced capacity or, eventually, shut down and cleaned. Optimizing heat exchanger maintenance requires identifying when to modify operations to extend heat exchanger life vs. when to take the heat exchanger offline for cleaning.
A major U.S. oil & gas firm was operating its heat exchangers on a set maintenance schedule, taking them offline every few months for cleaning. But this resulted in inefficiency and incurred unnecessary cost.
The refinery was interested in enabling risk-based heat exchanger maintenance planning and optimization of processing rates, operating costs, and maintenance costs. Before using Seeq, the engineers had to manually combine data entries in a spreadsheet and spend hours if not days formatting and filtering the content and removing non-relevant data (for example, when equipment was out of service).
Solution
Using Seeq, the refinery’s engineers were able to create a predictive model to anticipate when maintenance would next be required. The model also allowed them to investigate how changes in operating conditions could extend the time before maintenance. Additionally, Seeq made it easy to compare the current cycle with previous cycles to determine periods of accelerated fouling and diagnose the root causes.
The analysis was scaled out to monitor other heat exchangers at the refinery and other sites. Using Seeq to monitor heat exchanger performance in place of time-consuming spreadsheets eliminated weeks of work for engineers, freeing them up to perform other valuable tasks. The refinery expects to save millions of dollars per year as a result of improved turnaround planning and other improvement opportunities.
Results
The engineering solution drove long-term improvements for the refinery, including reduced production loss, at a savings of roughly $10,000 per year. In addition, migrating to risk-based maintenance planning reduced the impact on operations. Finally, this decreased the impact of unplanned rate reductions from heat-transfer constraints, enabling the refinery to avoid losing millions of dollars in opportunities from crude intermediate processing margins.
Data Sources
- Process Data Historian: OSIsoft PI, PHD, others.
- Heat Exchanger Design Data: Imported from the asset database or created in Seeq by engineer via scalars/signals.
- Thermodynamic data: Accessed via a lookup in Seeq or entered in Seeq by the engineer.
Data Cleansing
- Engineers can identify and remove irrelevant data from unit/equipment shutdowns as well as periods of abnormal operation to create a clean dataset for model generation.
Calculations and Conditions
- Capsules created with Seeq’s Value Search and Custom Condition tools identify downtimes and abnormal operation
- Engineers apply “first principles” equations to calculate the Heat Transfer Coefficient (U) from temperatures and flow rates with Seeq’s Formula tool.
- Seeq’s Prediction tool is used to develop a model of the U-value as a function of time.
Reporting and Collaboration
- Seeq reports the date on which the prediction intersects with the minimum allowed U performance threshold to enable fast prediction of end-of-life cycle. Additionally, in monitoring mode, the prediction is updated as new data is acquired.
- Users can better avoid operational challenges by enabling maintenance and operations teams to make informed decisions about when remove the exchanger from service to avoid unplanned shutdowns.
- Seeq’s Journal enables users to document detailed analysis steps for further review and process revisions.