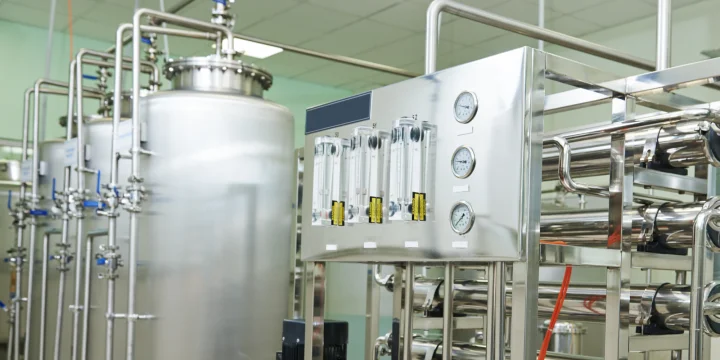
Filter Membrane Predictive Maintenance
Challenge
At manufacturing operations using ultrafiltration systems, the ultrafiltration membranes are used for numerous batches without replacement, using Clean-In- Place (CIP) operations in between batches to maintain filter performance. However, ineffective CIP cycles or long-term fouling or degradation of the filter membrane can result in increased cycle times to move the desired amount of product through the filter, lost yield as the product is unable to permeate the filter, or poor product quality as membrane failure may occur.
Solution
Companies using these systems turn to Seeq’s advanced analytics. Using context to separate product batch operation from cleaning operations, the data set during batch operation was isolated to provide context to how the filter was changing over time. In addition, Darcy’s Law was used to calculate and trend the membrane resistance over time, which is calculated based on the flow rates and pressures around the filter. A predictive maintenance model was created to extrapolate long-term degradation trends with warning and alert limits to plan maintenance periods prior to membrane failure.
Results
The ability to plan for maintenance of the filter membrane resulted in reduced impact to operations, saving both time and money. In addition, the replacement of membranes prior to significant degradation or failure resulted in reduced cycle time of filter operations, increased yield, and consistent batch quality.
Data Sources
- OSIsoft PI Platform
- SQL Database for UV Data
Data Cleansing
- Used UV Data and Flow Rates to determine when the filter was in operation, and specifically whether it was in cleaning or batch operation.
Calculations and Conditions
- Used Seeq’s Formula functions with Darcy’s Law to calculate membrane resistance during batch operation.
- Created prediction model to identify maintenance window.
Reporting and Collaboration
- Projected maintenance period was presented in Daily Meetings on Organizer Topic to plan an efficient time for maintenance prior to membrane failure or significant deterioration that impacts the process.