
Crystallization Deviation Investigation
Challenge
Small-molecule drug manufacture involves the batch processing of chemical compounds with the final step being their crystallization into a solid format. During a commercial campaign, a small-molecule pharmaceutical company needed to investigate the cause of crystallization deviations at the end of its batch processing. The time required for filtration exceeded the specifications – in one case more than doubling the filtration time — resulting in a deviation that suggested a quality problem.
The situation was serious, as deviations in crystallization threaten the integrity of the entire batch. According to industry research, batch failure from all causes occurs at a rate of roughly once per year in the pharmaceutical industry, and the costs can run in the millions of dollars.
Once a major deviation occurs, it can take days or weeks for the process to get back up and running as the team needs to prove they understand what happened and how it won’t happen it again. These delays are extremely costly. Timely production is key to satisfying market demands. No pharmaceutical manufacturer wants to be in a position of not supplying drugs to patients when needed. However, the quality and safety of the end product is paramount and overrides all other considerations.
It was critical to understand the root cause of the aberrations, allowing proactive mitigation.
The manufacturer’s engineering team was experiencing difficulty in trying to get to the root of the problem using spreadsheets. Differences in signal trends are difficult to spot with visualization and require extensive calculations that are difficult to perform with spreadsheets. For example, it is difficult to determine the energy balance on the crystallization profile using Excel. And the engineer would need to rebuild the calculations each time she wanted to evaluate a different time period. Spreadsheets were insufficient to meet the need for ease of use and speed of calculation.
Solution
- Identify a polymorph change using calculated heat of crystallization integral
- Alter the process to more consistently produce the desired polymorph
The root cause analysis was performed in Seeq to determine the changes that might explain the circumstances surrounding the slow-filtering batch. Using Seeq dramatically shortened the analysis time for the engineering team through integrative calculations and data analytics.
Whereas this type of analysis previously would take an engineer three full days to do, using Seeq, it took just four hours, a 6X improvement.
Through the use of Seeq tools, engineers identified a polymorph change from the calculated heat of crystallization integral for the deviated batch. A polymorph is a crystal property related to the size and shape of the molecular structure. The engineer leveraged differences between the desired polymorph and the undesired polymorph to alter the process to consistently produce the desired product.
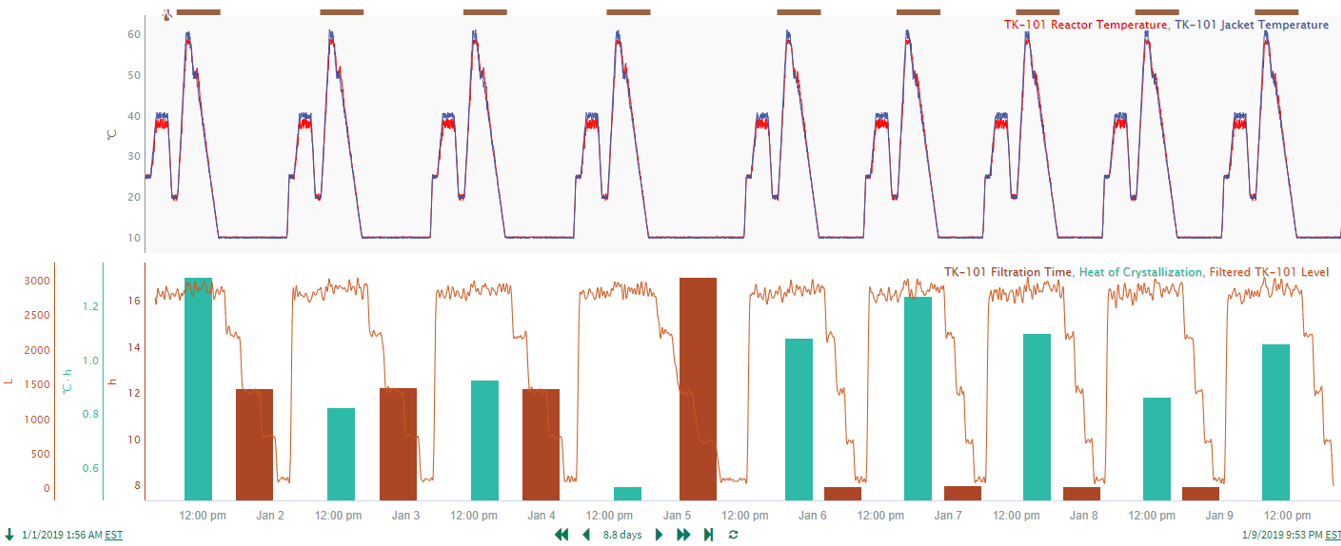
Data Sources
- OSIsoft PI
Data Cleansing
- Seeq automates the process of lining up data for calculations that may be recorded at different intervals.
- Filtering function performed on noisy level signal.
Calculations & Conditions
- Focused analysis on the desired operation of process (crystallization and filtration).
- Heat of crystallization estimated via the integral of the difference between jacket and contents temperature during crystallization.
Reporting & Collaboration
- The Seeq Organizer Topic is configured to auto-update as new data streams in to notify the operator on new stoppage events.
Results
The process engineering manager can share the findings with others on the team, including the production manager, to get input and to suggest mitigations. The whole team can collaborate and monitor all stoppages to determine if they were planned or unplanned.
Any time a common root cause comes to light, the team can change the process and then monitor it for the desired outcomes. This reduces the likelihood of unplanned outages and, therefore, the cost of production loss.