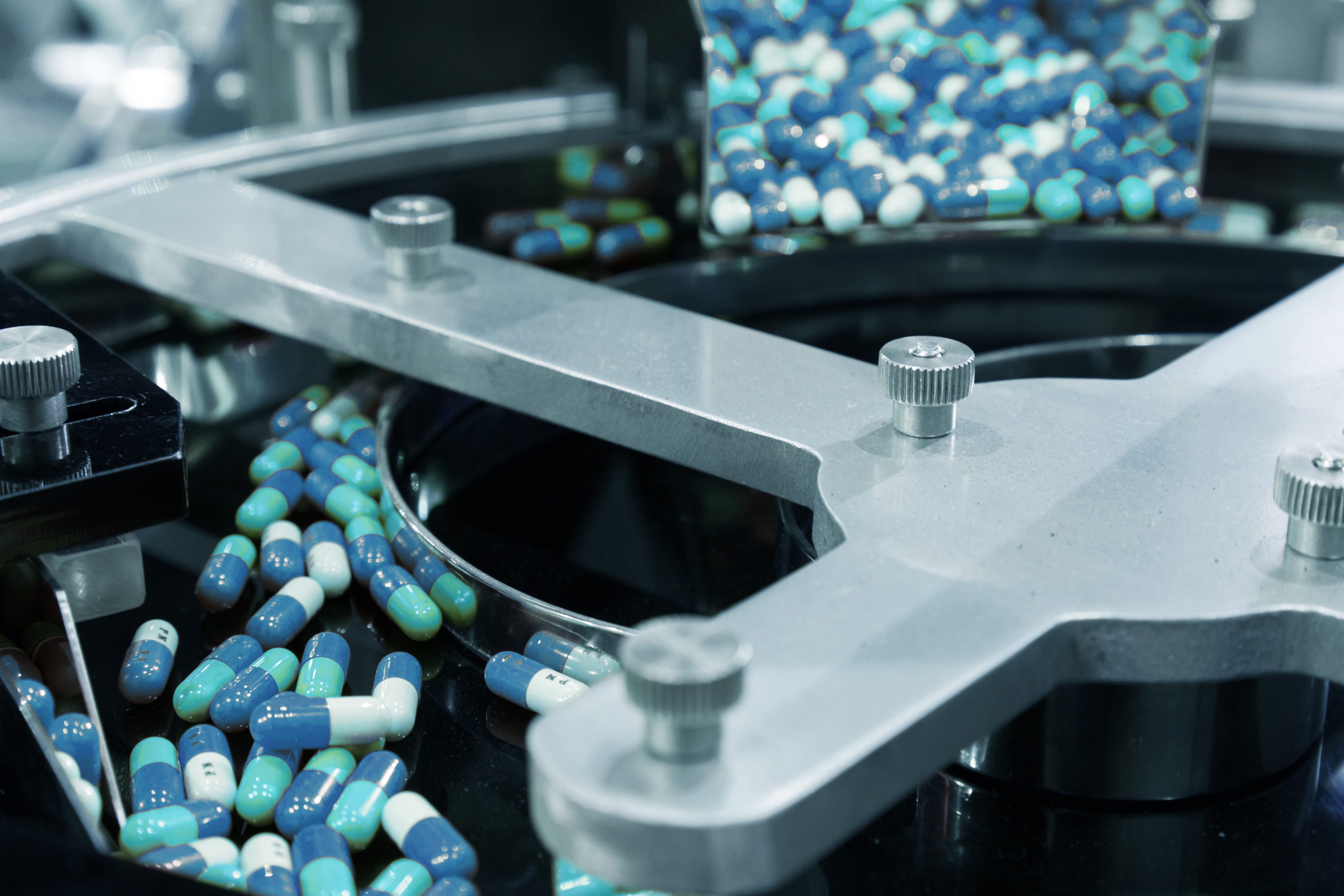
Continuous Manufacturing of Pharmaceuticals
Customer
Customer is a pharmaceutical company
Challenge
For more than 50 years, pharmaceuticals have been produced via batch manufacturing, which requires multiple steps and the use of large-scale equipment. Recently, however, many in the pharmaceutical industry have begun moving away from batch manufacturing to continuous manufacturing. The FDA is now taking proactive steps to facilitate the drug industry’s implementation of emerging technologies, including continuous manufacturing, to improve product quality and address many of the underlying causes of drug shortages and recalls.
The premise of continuous manufacturing of pharmaceuticals is that the ability to more tightly control processes will lead to better product quality, increasing efficiency, speeding time to market, and ultimately providing better protection of patient health.
In a continuous manufacturing process, it is often difficult to aggregate data to perform analytics across multiple assets, including process analytical technology (PAT) tools. In addition, continuous monitoring of key performance indicators (KPIs) in near-real-time is necessary to maintain the process within the desired design space. KPI monitoring is also needed to enable process adjustments prior to any variables trending outside of the design space.
A pharmaceutical company was finding it difficult to aggregate data and perform analytics across multiple assets, as well as monitor KPIs for continuous pharmaceutical processes in near-real-time. The company needed a dashboard to track and monitor the process parameters and identify deviations when they occur.
Solution
Using Seeq, the company’s quality engineers created a continuously updating operational dashboard to monitor KPIs. The dashboard enabled the engineers to easily identify deviations and trends outside tolerable ranges and calculate the time until manual operations (such as reagent loading) are needed. Among other KPIs, the dashboard tracks downtime deviations and idle time.
Seeq Organizer now monitors KPIs for the company’s entire continuous pharmaceutical process, enabling operators to view all process-relevant data in a convenient format on the production floor.
The dashboard identifies deviations from the design space parameter ranges, tracks downtime deviations and idle times, and calculates when manual operations such as reagent loading were required.
Data Sources
- OSIsoft PI
Data Cleansing
- Seeq can remove invalid data when a piece of equipment may be offline
- Shifted signals using time warping to line up material with equivalent quality data throughout the process
Calculations & Conditions
- Created conditions for deviations and idle time
- Calculated the estimated time until manual operations such as refilling reagent tanks are required
Reporting & Collaboration
- Color-coded dashboard created in Seeq Organizer for continuous process monitoring
- Standard daily process report created in Seeq Organizer for efficient data aggregation
Results
The dashboard enabled quality engineers to respond rapidly to production issues, thereby increasing product quality and process efficiency. The engineers also use the dashboard to view daily process-monitoring reports. The company saved an average of 30 minutes per day, per engineer, on reduced data aggregation time by utilizing Seeq, a significant time savings.