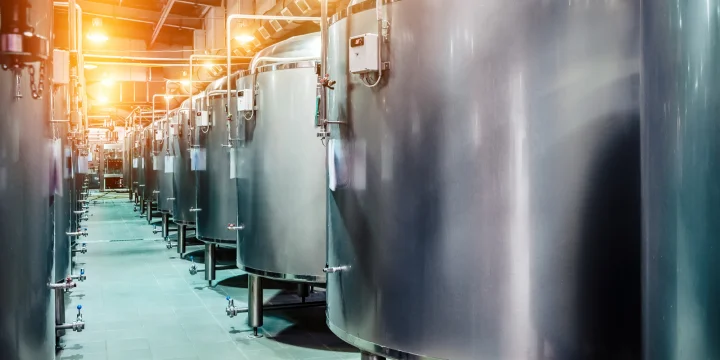
Batch Tracking & Cycle Time Analysis
Challenge
Batch manufacturing of chemicals entails many distinct phases. Chemicals manufacturers, therefore, strive to cut as much time as possible from each phase of the batch process. Shaving off even a small amount of time from a phase results in increased production, directly driving significant improvements in profitability.
A large chemical manufacturer was struggling to analyze batch phase times for process improvement using Excel spreadsheets. Spreadsheets have limitations that make them unsuited to this level of analysis. It was extremely difficult for the process engineering team to accurately define phases and idle times to pinpoint where to focus their process improvement efforts and capital deployments. Often, phase definitions were too complicated to analyze properly and resulted in capturing the wrong period, a frustrating waste of time. Analysis done on a spreadsheet was not easily sharable to others on the team.
It was also difficult if not impossible, to scale the analysis to all batches completed for more holistic insight. To perform cycle time analysis, an engineer would have to go back through thousands of batches in history to determine if the phase definitions were accurate for all phases of all batches, making it effectively unworkable.
Solution
Utilizing Seeq, process engineers can use process variables, formulas, and string signals to separate each batch into phases. This enables them to identify the “best” cycle time for each phase and tune production variables (such as adjusting pump speeds or adding catalysts sooner) to replicate the ideal cycle.
Seeq enables the team to define phases with process variables by using value search and formula, and apply those calculations to all batches in history. Engineers can flag phase durations that are abnormally long compared to historical averages, and systematically eliminate variability. They can monitor phase durations in operations meetings without manually updating spreadsheets.
Seeq gives engineers a visual indication of the time period they are capturing, for all their batches at once, an order of magnitude improvement over spreadsheets. Seeq gives the engineers immediate visual feedback as they adjust the time window, as opposed to just looking at numbers and timestamps in Excel. In addition, the team can produce a batch monitoring scorecard showing phase and idle duration to drive continuous improvement.
Seeq Journal enables the team to document the steps right next to the analysis, showing how they calculated the phases, making the analysis sustainable and easy to understand for future engineers.
Data Cleansing
- Filter noise from level, temperature, and flow signals
Calculations and Conditions
- Define phases for each step in the batch cycle using process variables
- Calculate the duration of each phase and compare to historical benchmarks
- Calculate the downtime for each phase and quantify the downtime as lost value
Reporting and Collaboration
- Dashboard with automatic updates to show phase duration of each batch
Results
Seeq helped the chemical manufacturer eliminate idle time within batches and time between batches. This enabled small improvements in cycle time and reduced batch-to-batch variation that have significant financial impact over time.
For example, if a process produces 10 batches per day, the cycle time per batch is 2.4 hours or 144 minutes, resulting in 3,640 batches per year. If through process improvement, the cycle time is improved by 10 minutes, the new batches/day rate would be 10.7 batches/day or 3,912 batches per year – almost 300 batches from an incremental improvement. With an average financial value ranging from $20,000 to $50,000 per batch, this is substantial. The company has achieved many improvements of this type with a major boost to profitability.