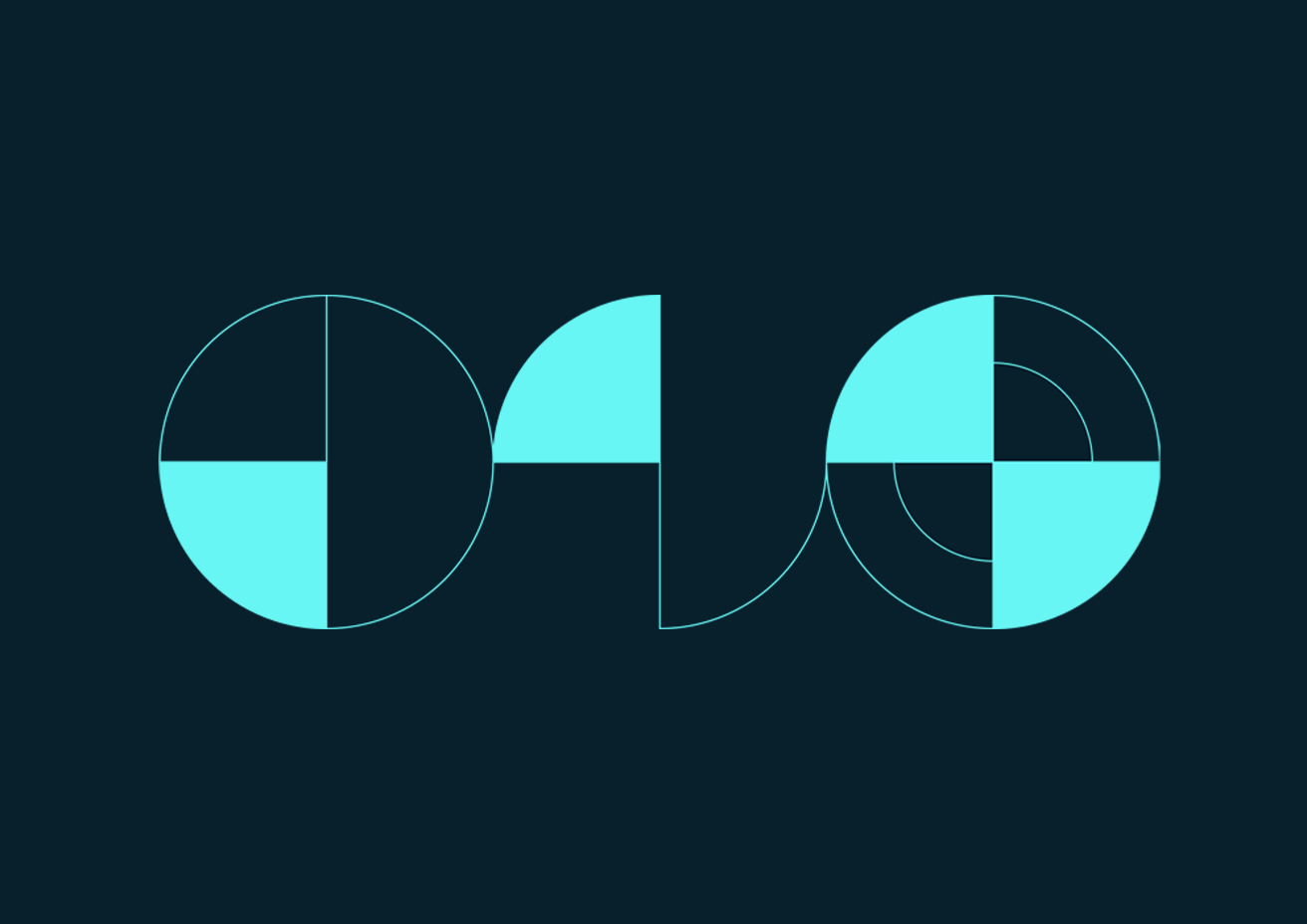
Seeqathon! 3 Days Generating Process Insights & Actions
A Sprint-Like Event Aimed at Developing Ready-to-Use Seeq Insights
Seeq customers know Seeq drives significant value for their organizations and they also know the ROI of their time spent using Seeq is quite high. However, simply finding time to develop high value insights using Seeq can be challenging because process engineers are so busy running their plants.
One of Seeq’s multinational chemical customers came up with a solution: Seeqathon, a 3-day event with two of their North American production sites. Motivated by the high value of the insights they have found using Seeq, they planned the event as a focused, fun time for their employees to collaborate, learn, and develop new Seeq worksheets and reports. Here’s how they defined it:
Seeqathon – a sprint-like event aimed at developing ready-to-use Seeq insights to address specific topics relevant to production sites. Participants are given the freedom to deal exclusively with these developments during the event. Emphasis is on focus, speed, and fun.
The customer’s internal Seeq sponsor and Seeq champions kicked off the Seeqathon on Day 1 with a review of scope, roles/responsibilities, and the overall objective:
Develop one or more functioning Seeq documents (workbenches, dashboards, etc.) per team by the end of the event. The best solution will be selected based on these criteria: usefulness, % completed, impact ($, quality, throughput), and creativity.
The overarching goal of Seeqathon was to give the process engineers dedicated time to hone their Seeq skills and develop insights with Seeq.
Approach and Results
Seeqathon participants were divided among 3 teams to work on their choice of a Seeq use case. The teams brainstormed, explored their data, and built new Seeq solutions over Days 1 and 2 of the competition. Internal Seeq champions and a Seeq Analytics Engineer were available during daily check-in/checkout meetings for questions and support.
Starting with only raw data (OSIsoft PI data servers, SQC data, etc.) and the team’s ideas on Day 1, the following categories of applications were rapidly developed and then demonstrated on Day 3:
- Process Quality Troubleshooting
- Equipment Performance
- Energy Modeling
- Process Compatibility Correlations
The company’s subject matter experts utilized a variety of Seeq features and tools in conjunction with their valuable process knowledge to generate the new process insights. The following table summarizes the key results by solution, as well as the main Seeq features used for each one:
Key Results for the New Seeqathon Applications | Features/Tools Used |
An investigation of batch quality issues found an unexpectedly strong correlation between raw material usage and the batch’s temperature exotherm peak. The identified correlation model can now be used for optimizing (reducing) batch cycle times (Figure 1). | Value Search
Signal from Condition Chain View Prediction |
Based on analytics results developed in Seeq using North American site data, one team extended their analysis by investigating process data for a raw material produced at an international site. | Multi data source connectivity |
Seeq enabled trending and analysis of SQC data alongside process historian data. This would have been very difficult otherwise and was essential to generating results for the Process Compatibility use case. The resulting tool correlates process and compatibility data, can be applied to many products, and shortens lead times for planning/customers. | Capsules/Conditions
CSV Import Reference Profile |
Analysis in Seeq confirmed a key performance difference between parallel assets. This finding will eliminate hours of processing time on equipment that is currently the process bottleneck (Figure 2). | Value Search
Signal from Condition Capsule View |
A sitewide energy model and associated energy dashboard were developed. The dashboard will be used for daily monitoring to identify excess/unexpected energy usage (highlighted via Scorecard Metric threshold colors), and to initiate further troubleshooting (Figure 3). | Value Search
Formula Prediction Periodic Condition Scorecard Metric Organizer Live Document |
Key process metrics were calculated using Seeq to determine equipment performance efficiency. This informed a decision to postpone scheduled cleaning and provided a quantitative method to schedule future cleanings. | Value Search
Signal from Condition Formula Chain View |
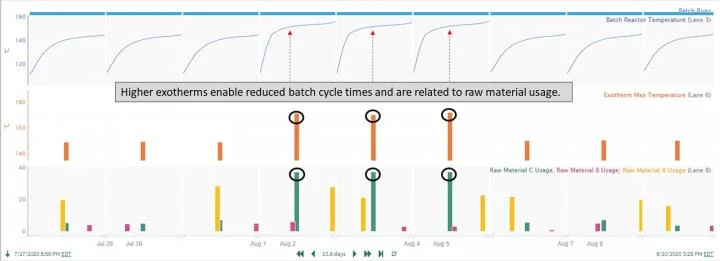
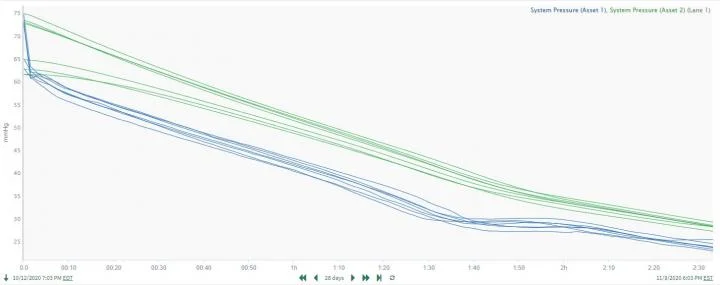
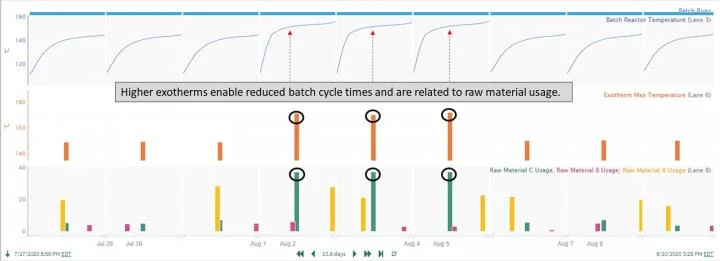
Following the final presentations, attended by 25 people including the customer’s Regional Manufacturing Director, everyone voted for the best application. The final votes were 9 to 8 to 8, a testament to the quality of the results generated by all 3 teams!
Top-down Support
This Seeqathon was a success and is typical of this type of internal event which benefit the entire ability spectrum from newly trained engineers to seasoned Seeq champions. They enable focused time free of distractions for collaboration, learning, and generating valuable insights into production, quality, energy use, and process safety. Corporate support is a key Seeqathon element which eliminates one of the biggest barriers to usage… “I don’t have dedicated time to work on use cases in Seeq.” Finally, Seeqathons complement other best practices such as:
- regular internal user forums where recent use cases are presented, users connect and collaborate across sites, and information is shared with the internal Seeq user community
- maintenance and promotion of internal customer shares which provide a central resource for file postings, questions and answers, recordings, and Seeq documentation
- capture of customer time savings and financial benefits from Seeq use case template slides summarizing the challenge, solution, and results
If you are interested in organizing a Seeqathon or similar event for your organization to provide a dedicated time and support for employees to use Seeq to uncover insights, we’d be happy to help. Contact us at [email protected] for more information.
Co-authored by John Cox and Nick Gigliotti, Analytics Engineers at Seeq Corporation.