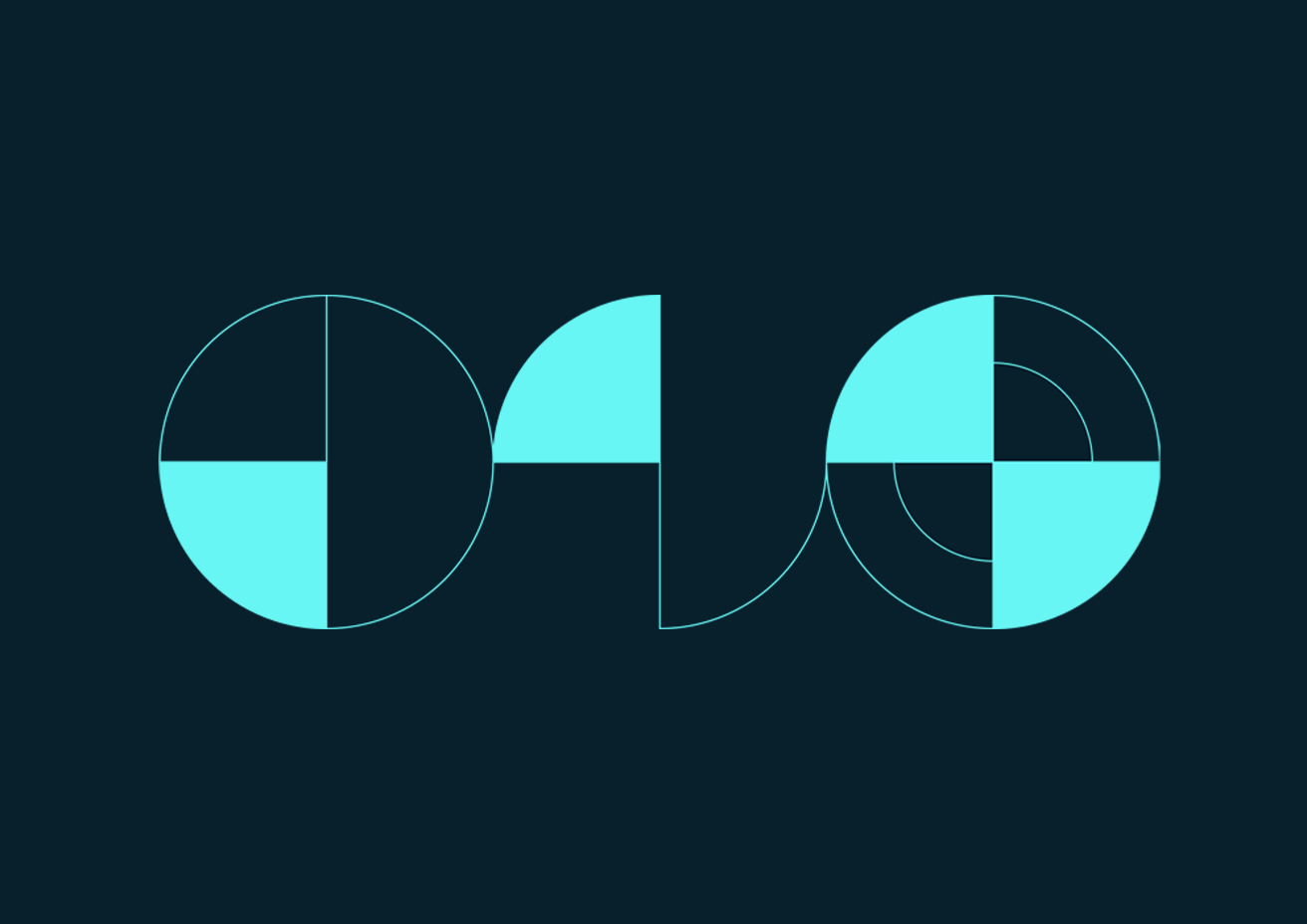
Advanced Analytics for Process Control Engineers
Leveraging Seeq to Drive Process Control Improvement
Process control engineers focus on optimizing the automatic control of the process operation, designing control strategies, specifying controller tuning, implementing advanced process control and real time optimization applications, and troubleshooting sources of abnormal process variation. In contrast to process engineers, control engineers focus much more on dynamic operational responses and signal trajectories. Control engineers often want to identify and analyze transient, non-steady modes of operation (e.g., setpoint ramps, startups, batch sequences, etc.)—for which Seeq’s extensive contextualization capabilities (capsules and conditions) were purposely built.
Process engineers and control engineers typically work in different roles within the process automation pyramid. While they both derive analytics value from Seeq’s contextualization and calculation tools, there are several capabilities that control engineers can specifically utilize for their unique roles.
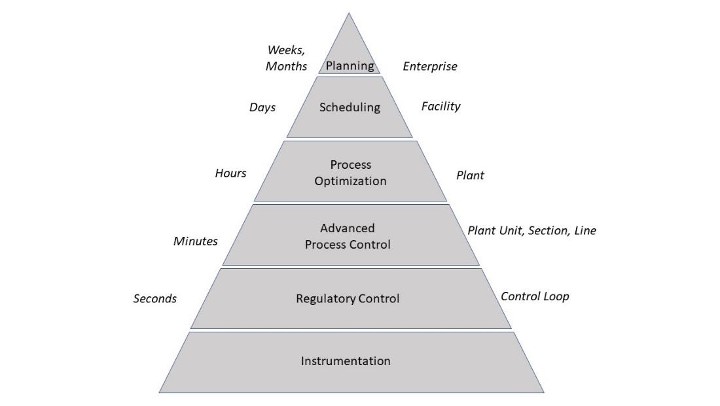
Evaluating and Reporting Automatic Control Benefits: Seeq’s Chain and Capsule View
The goal of process control improvement projects is almost always to reduce variability, lessen invasive corrections by operators, and positively impact production rate and energy usage. Seeq’s event identification and quantification tools make it easy to track benefits over time and across different operational states, enabling valid operation comparisons pre- and post-control improvement.
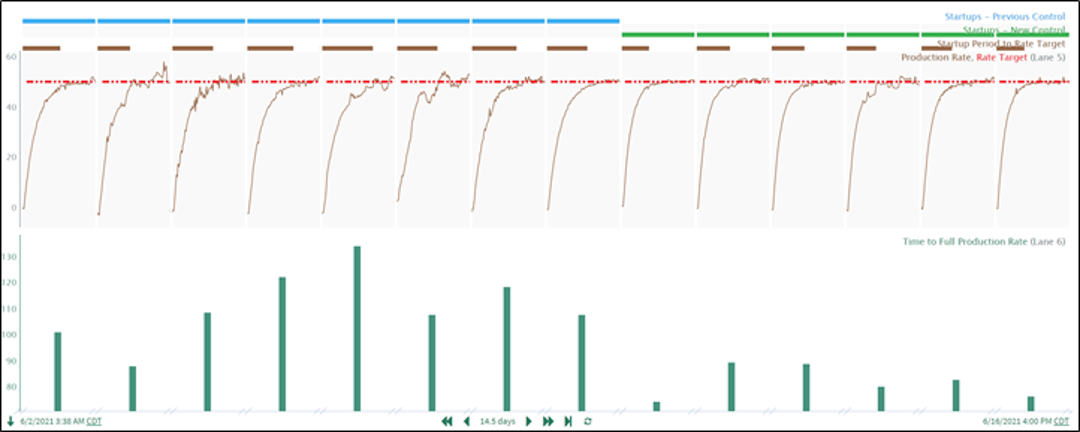
Process Variation Troubleshooting: Finding the Needle in the Haystack
When the process is operating abnormally, control engineers spend countless hours manually inspecting time series data trends for cause/effect relationships and anomalies. The following functionality makes process troubleshooting efforts much more time-efficient:
- Data cleansing approaches: downtime data removal, data filtering (smoothing), and operational mode searches
- Identifying process changes: benchmarking signal statistics across time periods to identify deviations from normal behavior; condensing critical signal behavior in chain or capsule view for easy visual inspection
- Causality (Seeq Add-on tool): generation of causal maps to guide cause and effect determination for large number of signals or complex processes
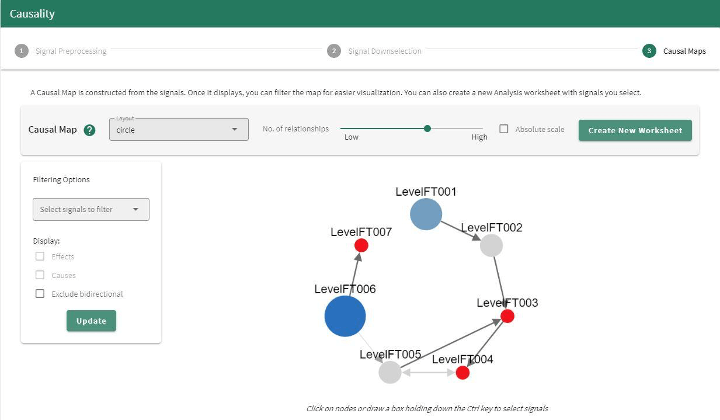
Dynamic Correlations and Modeling: Going Beyond Standard Prediction Modeling
Standard prediction modeling does not inherently handle process dynamics, or time-lagged signal correlations, which are often present in industrial processes due to liquid volume, transport delays, and equipment characteristics. Seeq’s Formula and extensibility tools provide approaches for typical dynamic modeling needs:
- Signal Alignment: a variety of methods can be used to align related upstream and downstream signals, such as process data and quality (lab) results
- Dynamic Modeling: The move() and exponentialFilter() Formula functions can be combined to generate first order and more complex dynamic responses. Use cases include:
- Dynamic model fitting of process gain, deadtime, and first order response time for PID controller tuning determination and advanced control implementation
- Real-time process estimation
- What-if analyses
- Correlation Analysis generates a correlation matrix summarizing the pairwise, maximized correlations and corresponding time shifts. This is useful for revealing time-lagged correlations in large datasets and creating time-shifted signals for further modeling and analysis in Workbench.
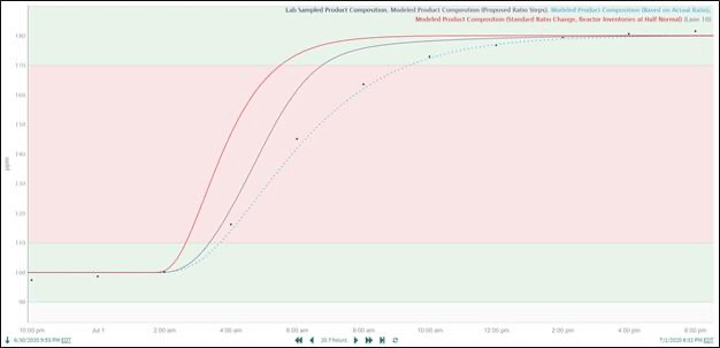
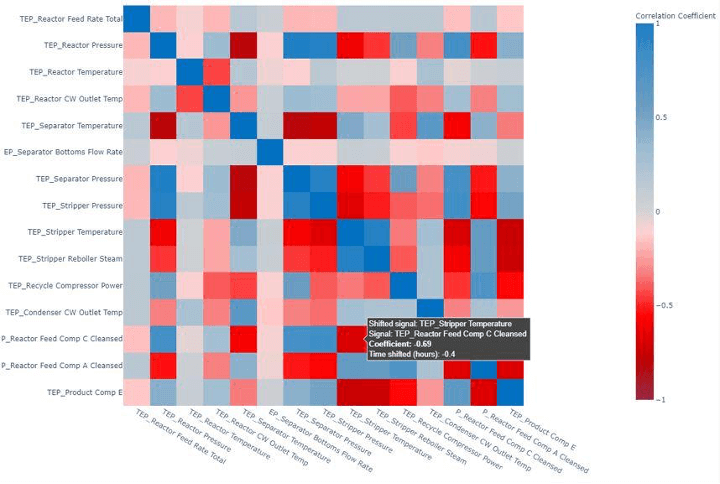
Control Loop Performance Monitoring
As part of the base regulatory control layer in Distributed Control Systems, the design and performance of PID controllers is key to transferring process variability to locations that do not adversely impact production rate and product quality. Therefore, automated monitoring of PID controller performance is essential to proactively identifying oscillations and other types of increased process variation which reduce economic performance. Seeq’s contextualization, Formula, and asset scaling features can be combined to automatically monitor individual controller performance as well as unit and plant level performance roll-ups. Just like pumps or reactors, PID controllers are assets. The asset-friendly experience in Seeq Workbench includes flexibility for asset performance monitoring, featuring: custom KPIs for controller performance, asset trees including controller importance, calculations roll-ups for higher-level monitoring, and more.
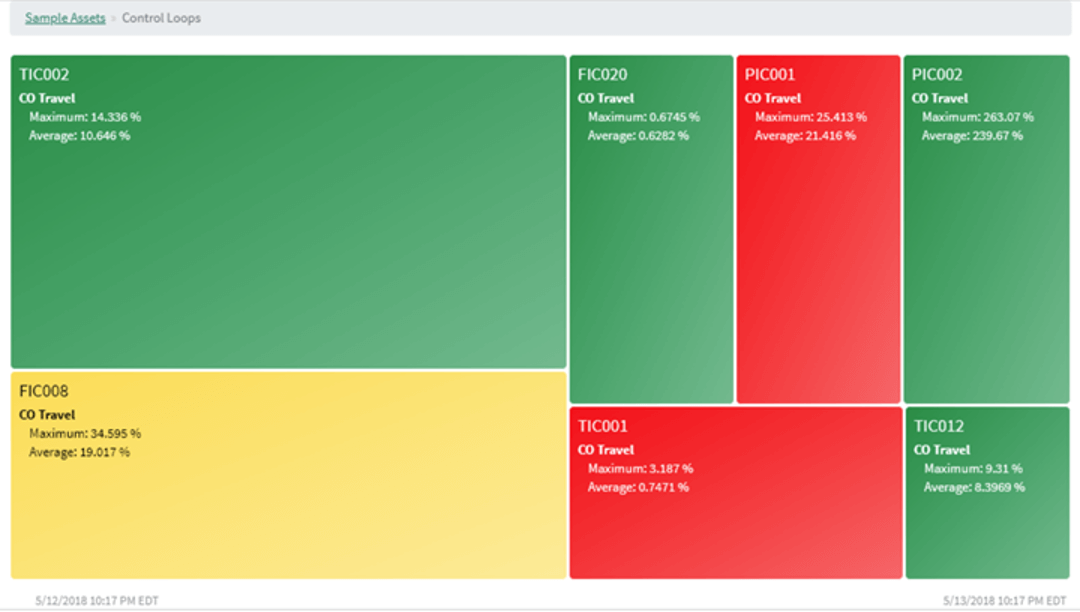
Advanced Process Control (APC) and Optimization
Control engineers often design advanced control applications to automatically operate the process in a more optimal way, running closer to process constraints to maximize production or minimize energy consumption. APC uptime monitoring and benefit $/index tracking are natural applications for Seeq. Identification of dynamic models (see Dynamic Correlations and Modeling, above) is an essential part of APC. Additionally, Seeq’s ability to connect to disparate data sources can help integrate planning and scheduling data with operational data for higher-level optimization analyses, and tools such as Parallel Coordinates can enhance APC visualizations.
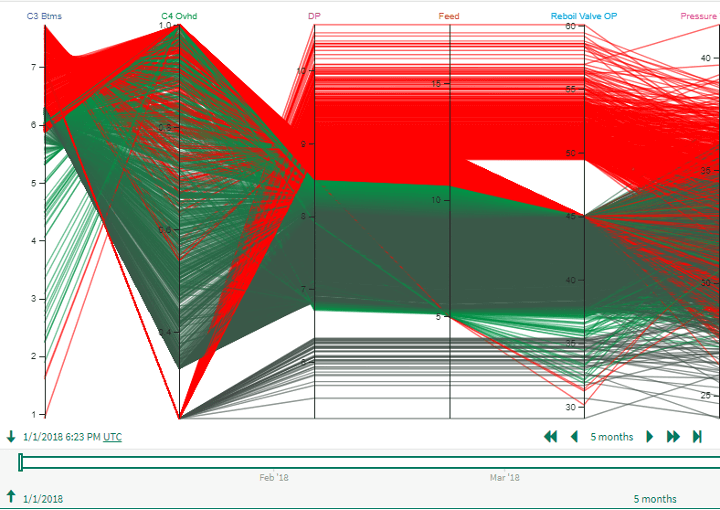
Monitoring Process and Quality Variation: Statistical Process Control (SPC) and Statistical Quality Control (SQC)
Closely related to control engineers’ focus on automatic feedback and feedforward control strategies, SPC and SQC are statistical techniques used to monitor, control, and improve the manufacturing process.
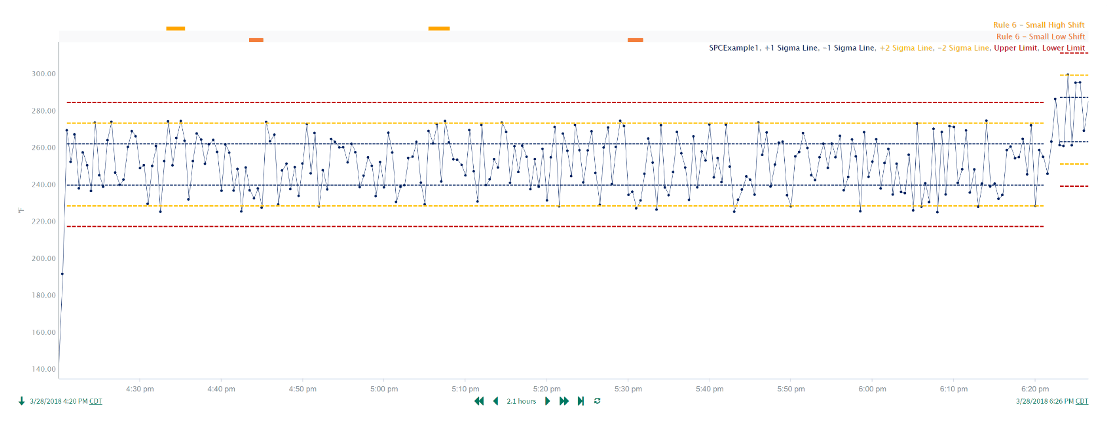
Deploying Seeq for Your Process Control Operations
Seeq isn’t just for process engineers—the leading advanced analytics application features many tools and approaches for process control focused analytics. While there are a number of solutions available for doing strictly process control analytics (such as controller performance monitoring), Seeq provides easy integration with other process data, user-developed custom performance metrics, state-based monitoring, and a collaborative experience where process control engineers can solve problems jointly with process engineering, reliability, and other team members. There is significant technical value derived from having control engineers’ dynamic analytics integrated within the same time series analytics application used by engineers, operators, and managers in all parts of the organization.
Download Seeq’s recent webinar for a deep dive into a variety of use cases that demonstrate how you can implement process control analytics and how using the same analytics solution across your organization can lead to better outcomes.
To see what Seeq will look like within your process control operations, schedule a live demo today.