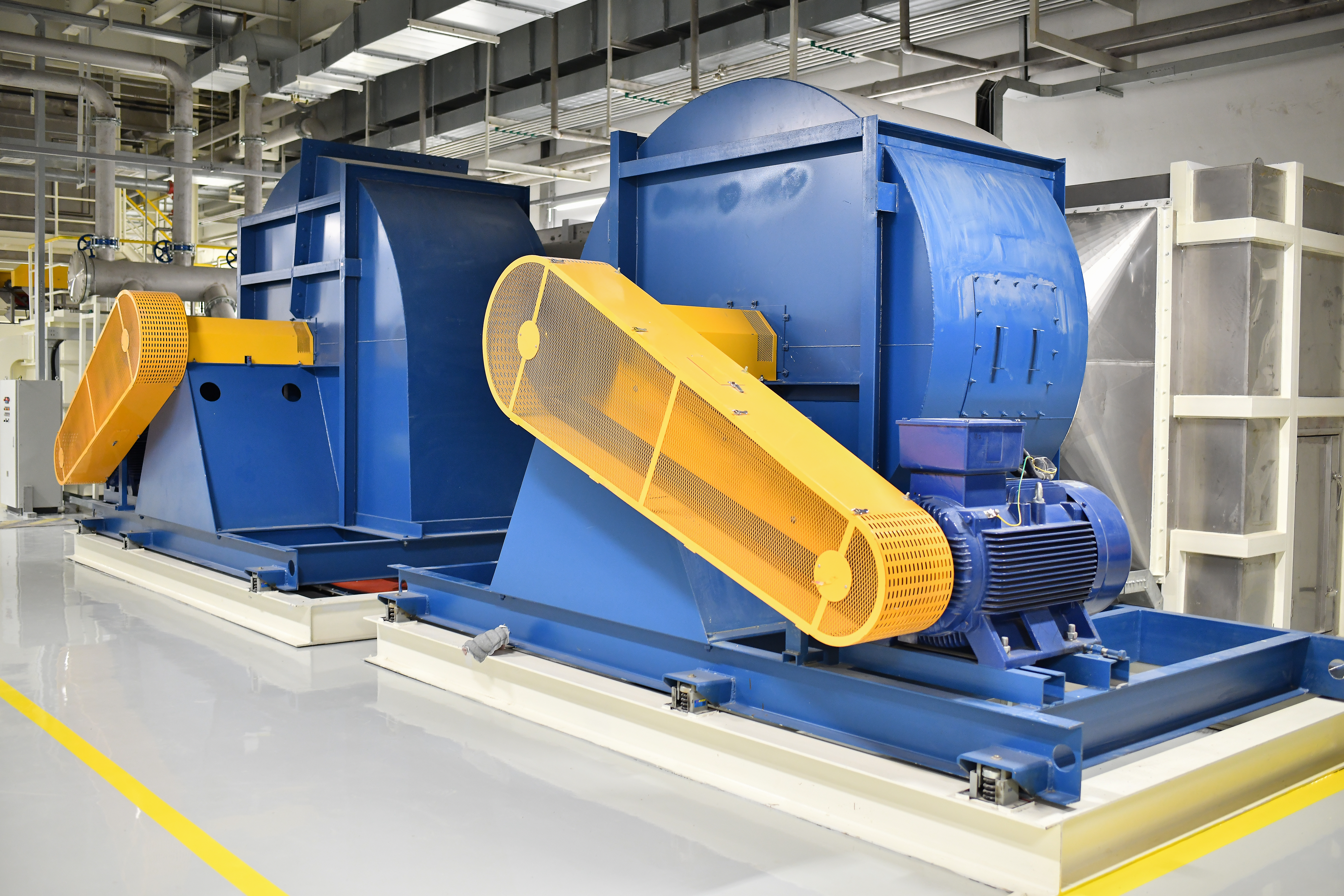
Induced-Draft Fan Maintenance
Customer
S&P 500 supplier of aggregates and heavy building materials
Challenge
Induced-draft fans are a critical part of the cement manufacturing process, creating a vacuum within the kiln to accelerate the drying process of clinker. Fans build up scales of dust on the blades over time, causing high vibration levels that can lead to the fans breaking down. Unplanned downtime of the induced-draft fans is extremely costly and cuts into profits. But cement companies also need to optimize planned maintenance for induced-draft fans so as not to waste resources.
An S&P 500 supplier of aggregates and heavy building materials needed a way to reduce unplanned downtime of its induced-draft fans. The cement company was experiencing an average of one full day of unplanned induced-draft fan downtime per quarter, at a significant cost of $20,000 per hour for a total cost of nearly $500,000. The company needed a way to greatly reduce or even eliminate unplanned induced-draft outages to maintain its profitability. The cement producer also needed a way to optimize its scheduled maintenance of induced draft fans as scheduled routine maintenance can be unnecessary and expensive.
There was no convenient way for the company’s reliability engineers to predict when the induced-draft fans would fail. It was too cumbersome and time-consuming to attempt to use spreadsheets to model when the fans were likely to fail.
Solution
Using Seeq advanced analytics, the team created a forecast model for condition-based monitoring of the induced-draft fans to plan maintenance before their vibration exceeds a critical limit.
Data Sources
- Wonderware Historian
- OSIsoft PI
Data Cleansing
- Vibration signal is filtered using Seeq Formula with agile filter
Calculations and Conditions
- Seeq’s Prediction tool creates a forecast for the vibration-based upon time since the last maintenance.
Reporting and Collaboration
- The reliability engineers and the maintenance scheduling people were able to share the condition-based monitoring reports with plant management for the first time.
Results
Seeq’s predictive capabilities use historical data from its data historian to inform scheduling maintenance to clean the dust scale build-up on the fan blades. This avoids the problem of taking equipment down too early, leading to unnecessary production loss, or waiting too long for maintenance, which risks unplanned rate reductions or shutdowns.
Seeq’s Prediction Tool integrates new data as it becomes available and modifies the predicted maintenance window accordingly. In addition, Seeq’s ability to overlay the current operating cycle with past operating cycles aids identification and troubleshooting of vibration events. This reduces the likelihood of unplanned outages, helping it avoid the cost of roughly $20,000 per hour. The condition monitoring of the induced-draft fans enables the cement company to optimize its maintenance.