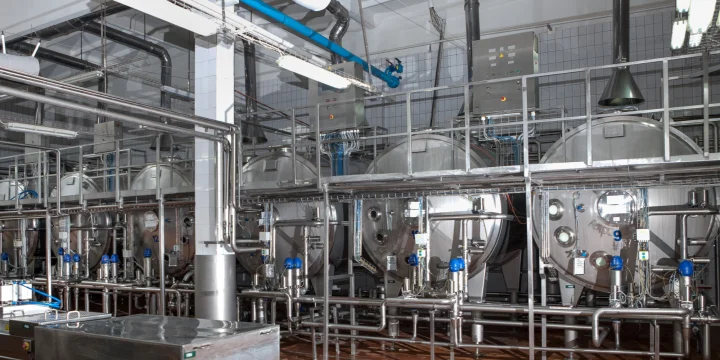
Clean in Place (CIP) Optimization
Challenge
Reducing the amount of time and resources spent for clean-in-place (CIP) operations increases overall production. However, there are several challenges to effectively analyzing CIP operations, including: identifying when cleaning is taking place from the data, quantifying results and raw material usage, distributing knowledge of specific abnormal occurrences, and increasing awareness of loss of consistent operations.
Solution
Seeq Tools help to create a process model that can be easily applied across different cleaning circuits and amended with circuit specific data. With the model, an engineer can easily compare effluent water quality for different cycles and across different circuits. Users can also determine the cause of excessively long cleaning periods. Using Seeq Journal, engineers can create summary reports of cleaning periods and dashboards to monitor day-to-day cleaning operation.
Benefits
Companies who use Seeq benefit from a clear CIP visualization which allows for troubleshooting of root causes. Overall consistency can be improved and CIP duration can be significantly reduced resulting in increased production.
Data Sources
- OSI PI and PI Asset Framework
Data Cleansing
Seeq enables continual contextualization of process data, enabling engineers to create accurate process signal statistics across each mode of operation.
Calculations and Capsules
With Seeq, engineers can develop capsules that detect different process phases including production and cleaning. They can calculate key metrics, including the total time and % per phase, cleaning time, and peak conductivity in cleaning cycle. Seeq tools can easily create an operational dashboard that includes a cycle-to-cycle comparison as well as circuit-to-circuit comparison. If desired, all data can be exported to PowerBI seamlessly to generate a management dashboard.
Summarizing Results
Seeq allows for quick determination of cleaning cycles that are longer than normal and identification of the root cause of such exceedances, identifying improvement opportunities which result in a reduction in cleaning cycle time and increased production.