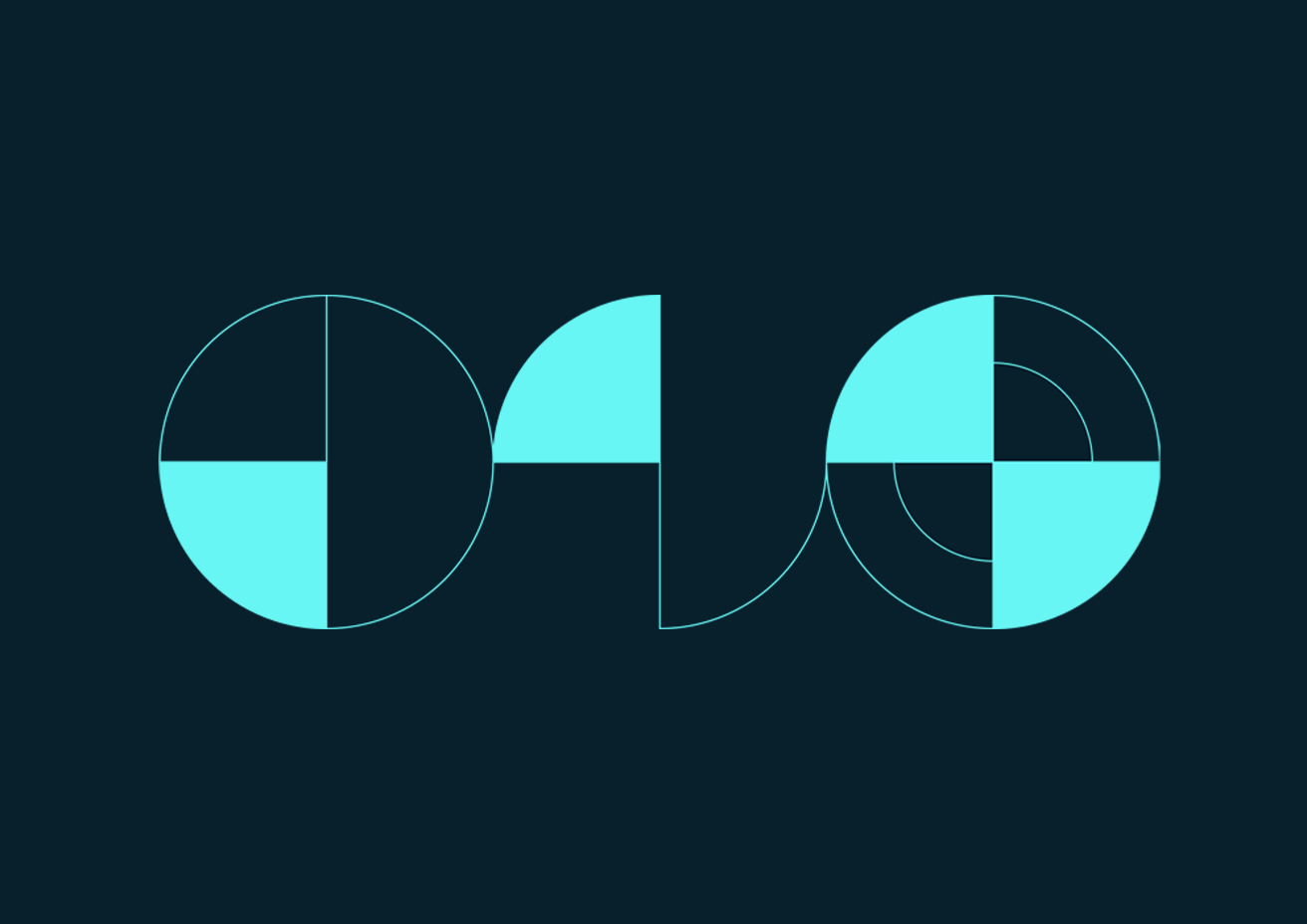
The Future of Lean: Seeq’s Advanced Analytics Revitalize Six Sigma
How to Use Advanced Analytics to Revitalize Six Sigma
Lean and Six Sigma continuous improvement methodologies have been a foundation in process manufacturing industries for decades. In more recent times, industry 4.0 and data science innovations—such as machine learning, big data, and cloud computing—have improved analytic capabilities beyond historical limits, enabling the evolution of Lean and Six Sigma efforts. However, the foundational Six Sigma methodology of define, measure, analyze, improve, control (DMAIC) has remained the same.
DMAIC is typically used by certified Six Sigma Black Belts to solve well-defined process optimization problems. The challenge is DMAIC analytics can result in organizational and data silos based on where the Black Belts are deployed. A more modern approach is enabled with Seeq which democratizes data and analytics across organizations, empowering an army of DMAIC practitioners to use advanced statistical concepts to solve manufacturing problems—with no Black Belt required.
Leaning into digital lean with Seeq
Seeq advanced analytics are expanding existing process improvement frameworks to include new and previously unsolvable use cases. While many time series analytics applications are shaped by the DMAIC process, Seeq follows a less regimented version of the DMAIC workflow, providing flexibility and agility in objectives and approaches.
Seeq empowers process engineers, shift supervisors, and other experienced subject matter experts (SMEs) to:
- Define and document use case background, challenges, and criteria for success.
- Identify measured variables and contextual information necessary to solve the problem via live data connection.
- Cleanse and contextualize data to analyze relevant information, calculate KPIs, and create predictive models to indicate anomalies.
- Apply resulting models, calculations, and monitoring techniques to improve methods.
- Operationalize insights so front-line personnel can make proactive process adjustments to control product quality, throughput rates, and equipment performance.
Reducing time to insight
With data driven problem solving, users must first define key objectives to generate business value. They can then identify the data required, specify where it is stored, and detail how it is accessed.
Seeq streamlines this process by connecting directly to systems of record and enabling users to cleanse, contextualize, and model data without being limited to rows in a spreadsheet. With Seeq, visualizing data, detecting events, cleansing signals, performing statistical calculations, and creating multivariate models is faster and easier. Putting data in context, another critical step, is simple with Seeq (Figure 1).
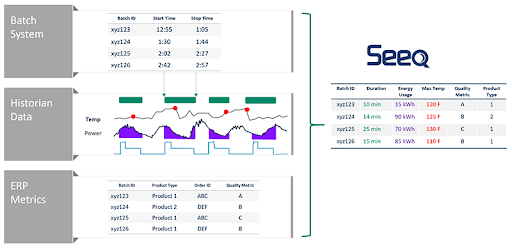
Once users understand the data required, they can identify pre-defined time ranges; unique operating modes; patterns in a trend, batch or procedural sequence; operating limit deviations, or any combination of these and other events.
Seeq enables rapid event detection and subsequent creation of visual representations. From there, users can build advanced regression models, create golden profiles, and more. If a use case warrants ML or AI algorithms, Seeq users can also leverage Python or other programming languages.
Iteration and collaboration
The improvement and control phases are iterative for any data-driven operational excellence project. The initial deployment of an analytical model or other process improvement project is validated and improved by testing against historical and incoming data sets. SME participation is critical to ensure appropriate test data sets and weed out one-off events.
To improve this iterative process, Seeq enables real-time collaboration for sharing, analyzing, and documenting results among employees. These results can then inform rapid process adjustments to achieve the stated business objectives.
Use Case: Process improvement using Seeq and DMAIC
A large petrochemical manufacturer had difficulty controlling product quality, resulting in product downgrades and wasted raw materials. Using the DMAIC process improvement methodology and Seeq, the company implemented a product quality control strategy using predictive modeling. The solution saved one production line $500k per year in margin loss.
- Define: A team of process SMEs identified necessary data, along with the time range comprising a historical dataset representing multiple modes of operation and product types. Their goal was to deploy a product quality model to prescribe proactive adjustments which would significantly improve product quality downgrades.
- Measure: Using Seeq’s out-of-the-box connectors, they created a live connection to the process data historian and laboratory information management systems. By using unmanipulated source data, they ensured no critical data would be ignored because of down sampling or aggregation.
- Analyze: Raw process signals were cleansed, time-delayed, and overlaid with the product quality data. The team built a regression model of the quality parameter using the delayed process signals. The model gave operations and engineering insight into product quality results, well before the sample was taken for the measured test (Figure 2).
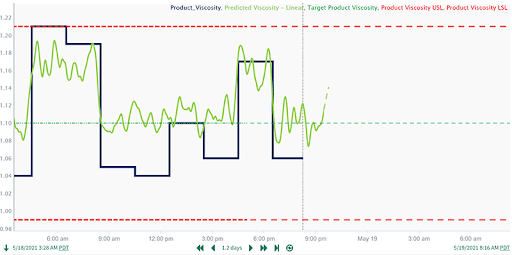
- Improve – Model performance was evaluated using historical data outside of the training dataset, and it was discovered that the model performed poorly for a couple of infrequently run product types. The decision was made to produce a series of product specific models, and to stitch them together into a single final model for deployment.
- Control – The online model, combined with the expertise of front-line operators and engineers, resulted in adoption of a new and improved control methodology for this product quality parameter. Rather than waiting on the results of a lab test hours in the future, operators seeing a predicted low-quality result were empowered to investigate, act, and evaluate the results of their actions on the quality prediction.
Lean and Six Sigma projects have served the process industries well for decades. Thanks to Seeq’s self-service advanced analytics capabilities, users are combining new technologies with DMAIC processes to optimize production, quality, and sustainability outcomes.
FAQ
How does Seeq empower process engineers?
- Define and document use case background, challenges, and criteria for success.
- Identify measured variables and contextual information necessary to solve the problem via live data connection.
- Cleanse and contextualize data to analyze relevant information, calculate KPIs, and create predictive models to indicate anomalies.
- Apply resulting models, calculations, and monitoring techniques to improve methods.
- Operationalize insights so front-line personnel can make proactive process adjustments to control product quality, throughput rates, and equipment performance.
How can Seeq and DMAIC save you time and money?
- Define and document use case background, challenges, and criteria for success.
- Identify measured variables and contextual information necessary to solve the problem via live data connection.
- Cleanse and contextualize data to analyze relevant information, calculate KPIs, and create predictive models to indicate anomalies.
- Apply resulting models, calculations, and monitoring techniques to improve methods.
- Operationalize insights so front-line personnel can make proactive process adjustments to control product quality, throughput rates, and equipment performance.